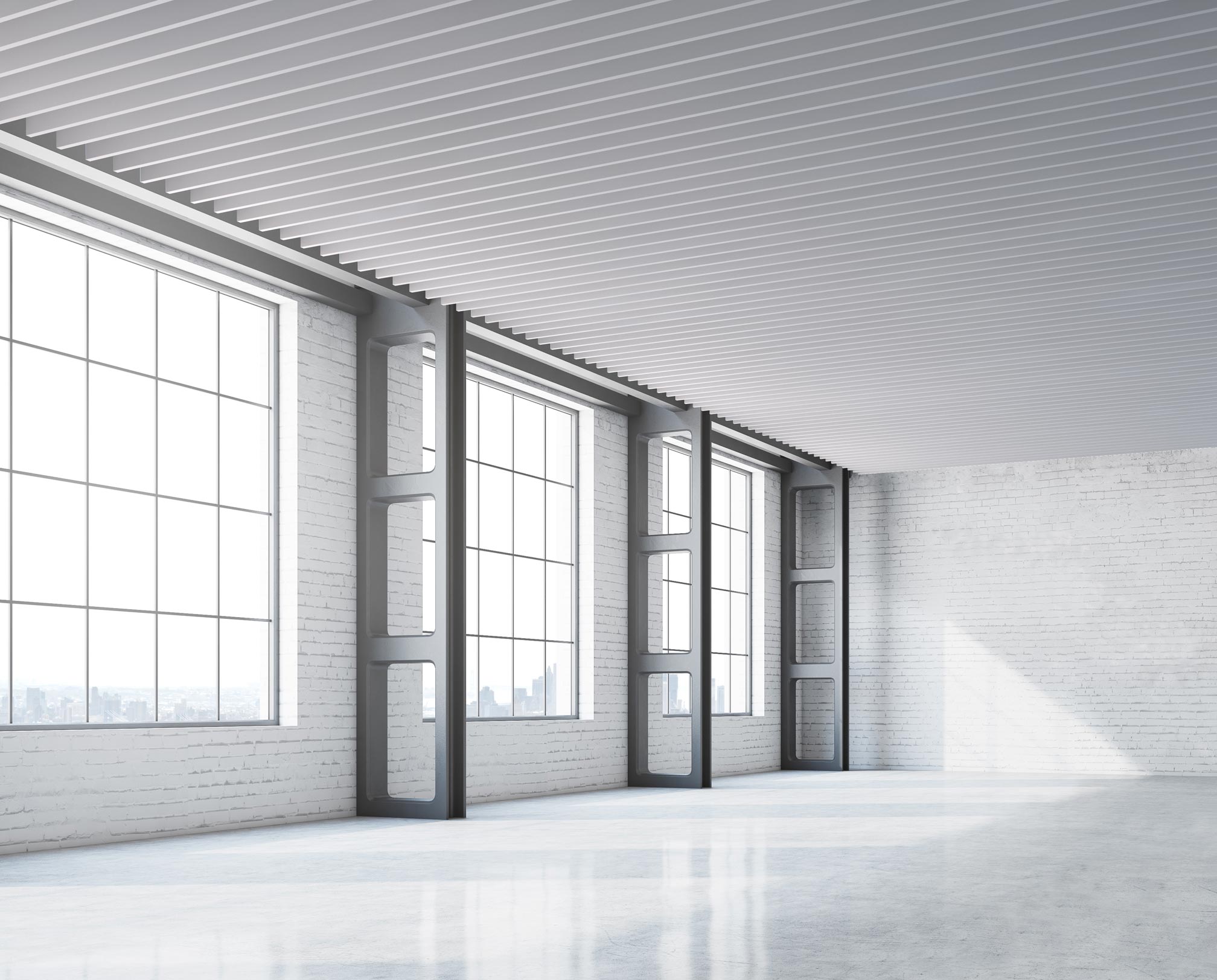
Aluminium is renowned for its many qualities, including lightness and strength. While untreated extrusions can be aesthetically pleasing, at MBS Architectural, we recommend that you either powder coat or anodise your Aluminium Batten. While the primary role of these finishing methods is to add colour, they also boost corrosion resistance, add hardness to the material and improve batten durability.
Powder coating and anodising each offer unique advantages. Read below to learn more about each finishing method.
Powder Coating
By far the most common method of finishing an aluminium batten. Powder coating is an electrostatic process of applying a dry powder to the aluminium surface before curing this extrusion under ultraviolet light or heat. The electrostatic process charges the extrusion, allowing the powder to fuse to its surface.
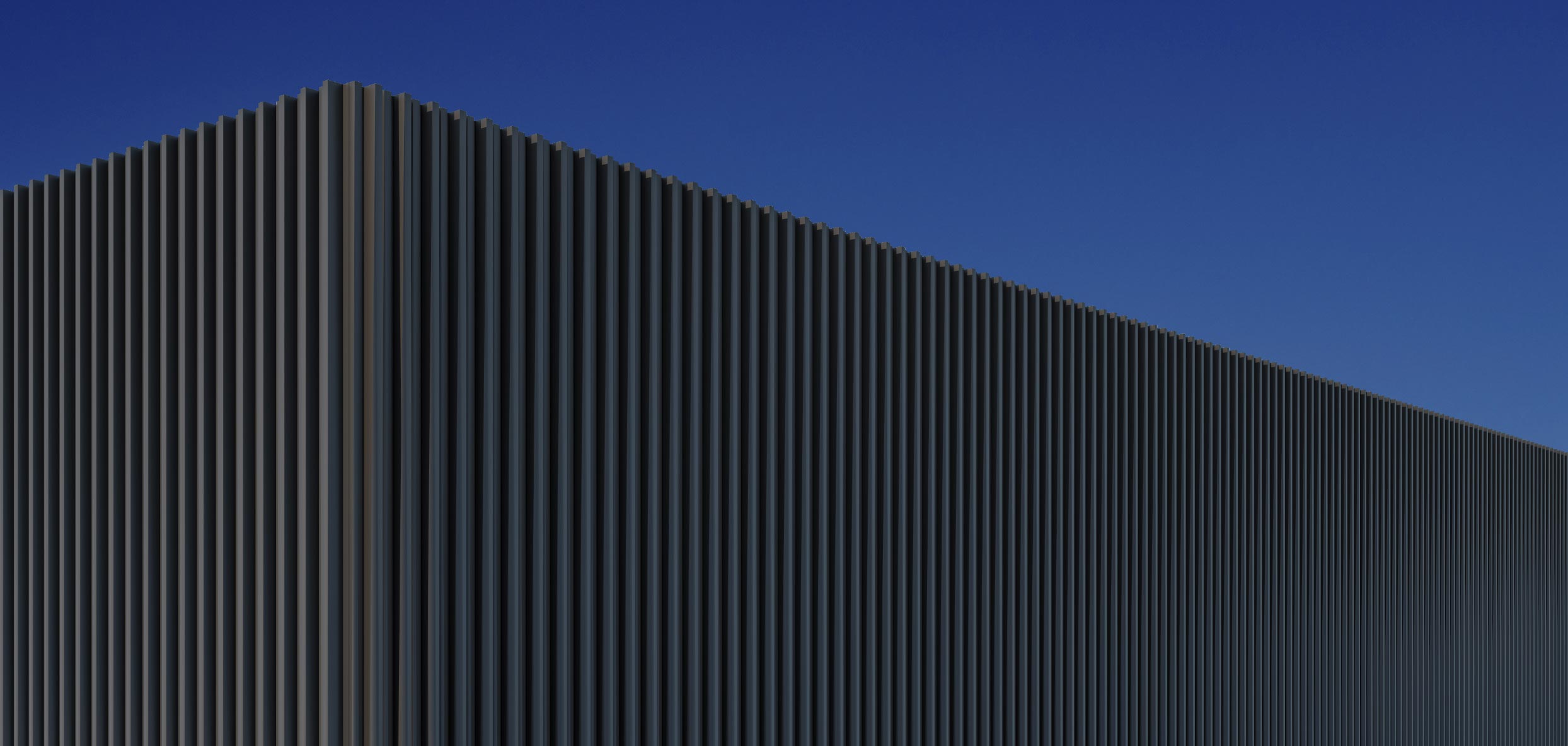
Advantages of Powder Coating
⤷ Consistent colouring
⤷ Material can be added years down the track, finished in the same colour and will appear the same as previously installed material
⤷ Easy to replicate colour in touch-up paint to repair scratches or damage
⤷ It can achieve a substantially thicker coating. Important in applications where a large amount of work has been done to the aluminium surface (Eg. Curving an aluminium batten)
⤷ Most extensive range of colours available (see Interpon and Dulux)
⤷ Many powder coats exist that are intended to mimic other materials or finishes. E.g. Anodising, Timber, Concrete, Marble etc.
⤷ Powder coating is a non-toxic finish
⤷ Typically the most cost-effective finishing method
Disadvantages of Powder Coating
⤷ Dry powders cannot be mixed to create unique colours
⤷ Minimum order quantities apply
⤷ Appropriate pre-treating of material is required to achieve a clean and neat finished material
⤷ Difficult to achieve a thin finishing layer
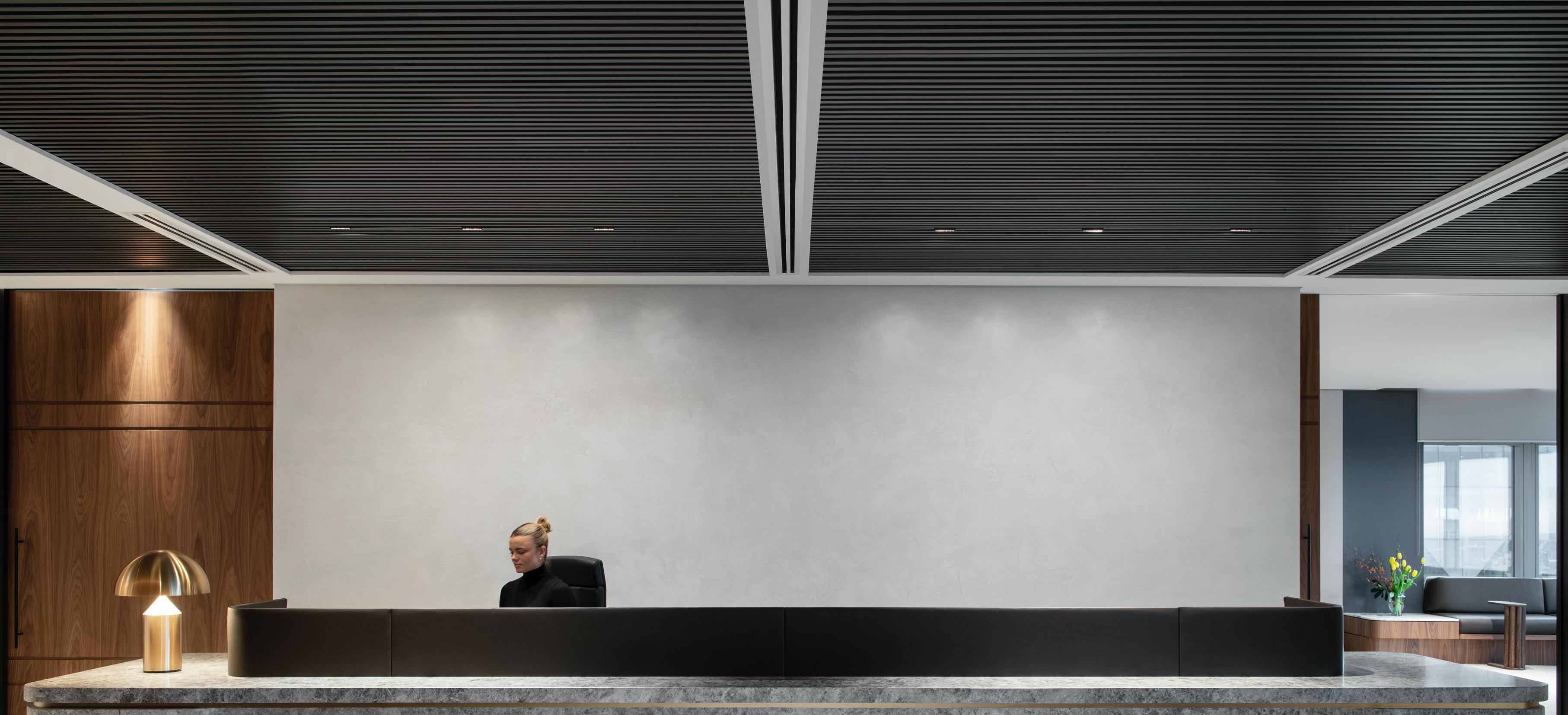
Anodising
Anodising is becoming increasingly popular in interior aluminium batten applications and is a finishing method that involves an electrochemical process. In simple terms, anodising is a process of highly controlled oxidation. On an aluminium batten, the process is achieved by immersing the batten profile into a large bath. This bath consists of an acid electrolyte, and a cathode is also mounted to the inside of this bath. Once immersed, an electric current is passed through the bath. In this instance, the Aluminium acts as an anode, and the cathode is the electrode where the reduction occurs, allowing the oxygen ions that are omitted from the electrolyte to combine with the atoms on the surface of the Aluminium.
As the finishing method is essentially controlling the level of oxidation, the length of time that the aluminium batten profile is immersed within the bath is critical to ensuring the anodised finish level.
Advantages of Anodising
⤷ Anodised materials are typically easier to maintain and are easy to clean to return to their original lustre
⤷ Some fantastic colour options are only available in this anodising finishing method
⤷ Unlike powder coating, this finish does not sit on the surface. It becomes a part of the aluminium substrate. Consequently, it will not flake or peel over its lifetime.
Disadvantages of Anodising
⤷ Not suitable for all grades of Aluminium
⤷ Highly subject to colour variations! **Important to be aware of
⤷ Hard to replicate colour consistency between batches
⤷ More expensive than other finishing methods
⤷ It can only be applied to Aluminium
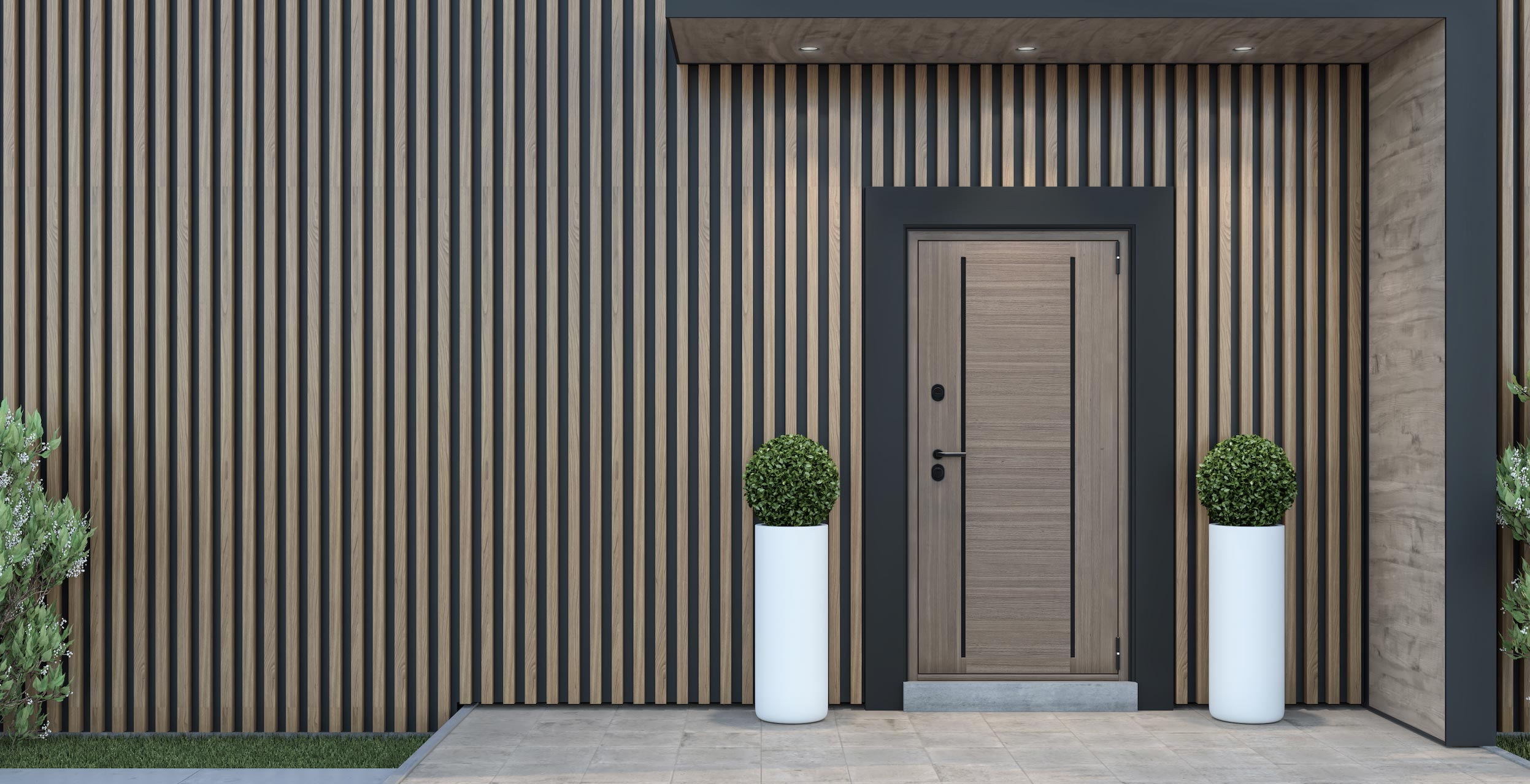
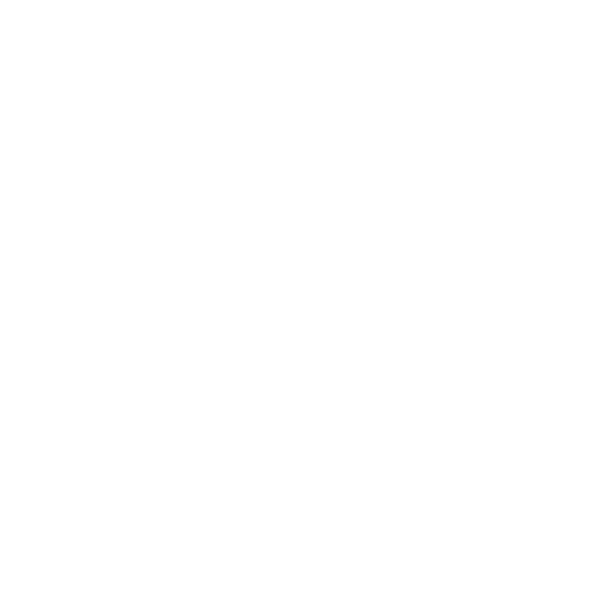
Book a call with our architectural team today to get down into the detail. We are happy to chat through ideas, materiality and budget to find out how we can help you create the interiors you need. Simply drop us a note on hello@mbsarchitectural.com.au or call us on 03 9580 7800 to chat with our specification team.
Every material.one source.
Let's bring your project to life.